Mechanical seals play a very important role in avoiding the leakage for many different industries. In the marine industry there are pump mechanical seals, rotating shaft mechanical seals. And in the oil and gas industry there are cartridge mechanical seals, split mechanical seals or dry gas mechanical seals. In the car industries there are water mechanical seals. And in the chemical industry there are mixer mechanical seals (agitator mechanical seals) and compressor mechanical seals.
Depend on different using condition, it require the mechanical sealing solution with different material. There are many kinds of material used in the mechanical shaft seals such as ceramic mechanical seals, carbon mechanical seals, Silicone carbide mechanical seals, SSIC mechanical seals and TC mechanical seals.
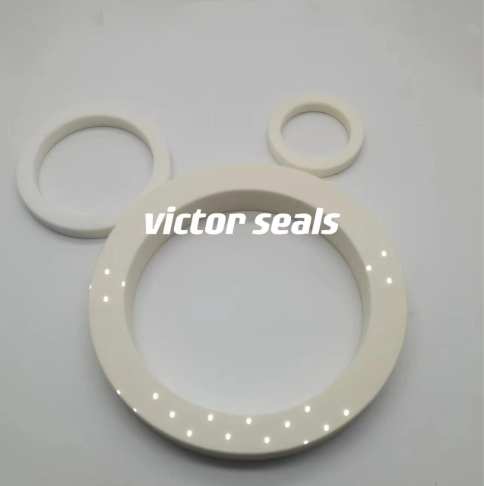
Ceramic mechanical seals
Ceramic mechanical seals are critical components in various industrial applications, designed to prevent leakage of fluids between two surfaces, such as a rotating shaft and a stationary housing. These seals are highly valued for their exceptional wear resistance, corrosion resistance, and ability to withstand extreme temperatures.
The primary role of ceramic mechanical seals is to maintain the integrity of equipment by preventing fluid loss or contamination. They are used in numerous industries, including oil and gas, chemical processing, water treatment, pharmaceuticals, and food processing. The widespread use of these seals can be attributed to their durable construction; they are made from advanced ceramic materials that offer superior performance characteristics compared to other seal materials.
Ceramic mechanical seals comprise two main components: one is a mechanical stationary face (usually made of ceramic material), and another is a mechanical rotary face (commonly constructed from carbon graphite). The sealing action occurs when both faces are pressed together using a spring force, creating an effective barrier against fluid leakage. As the equipment operates, the lubricating film between the sealing faces reduces friction and wear while maintaining a tight seal.
One crucial factor that sets apart ceramic mechanical seals from other types is their outstanding resistance to wear. Ceramic materials possess excellent hardness properties which allow them to endure abrasive conditions without significant damage. This results in longer-lasting seals that require less frequent replacement or maintenance than those made from softer materials.
In addition to wear resistance, ceramics also exhibit exceptional thermal stability. They can withstand high temperatures without experiencing degradation or losing their sealing efficiency. This makes them suitable for use in high-temperature applications where other seal materials might fail prematurely.
Lastly, ceramic mechanical seals offer excellent chemical compatibility, with resistance to various corrosive substances. This makes them an attractive choice for industries that routinely deal with harsh chemicals and aggressive fluids.
Ceramic mechanical seals are essential component seals designed to prevent fluid leakage in industrial equipment. Their unique properties, such as wear resistance, thermal stability, and chemical compatibility, make them a preferred choice for various applications across multiple industries
ceramic physical property |
||||
Technical parameter |
unit |
95% |
99% |
99.50% |
Density |
g/cm3 |
3.7 |
3.88 |
3.9 |
Hardness |
HRA |
85 |
88 |
90 |
Porosity rate |
% |
0.4 |
0.2 |
0.15 |
Fractural strength |
MPa |
250 |
310 |
350 |
Coefficient of heat expansion |
10(-6)/K |
5.5 |
5.3 |
5.2 |
Thermal conductivity |
W/M.K |
27.8 |
26.7 |
26 |
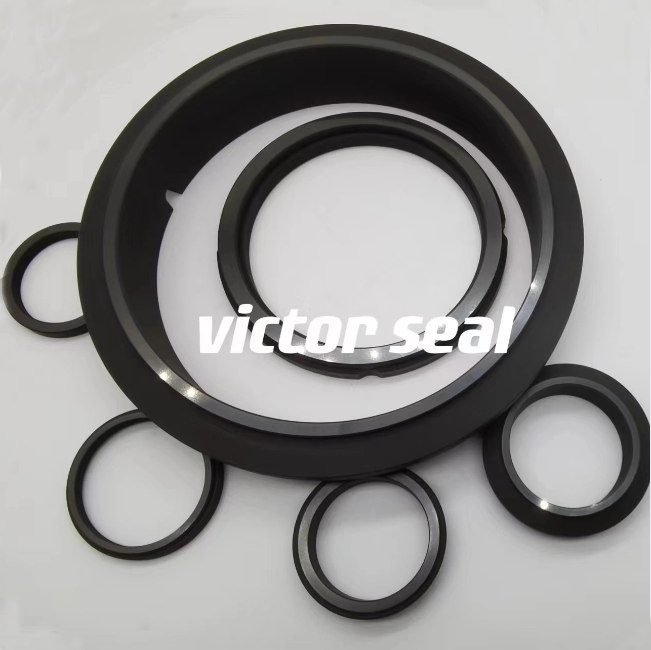
Carbon mechanical seals
Mechanical carbon seal has a long history. Graphite is an isoform of element carbon. In 1971, the United States studied the successful flexible graphite mechanical sealing material, which solved the leakage of atomic energy valve. After deep processing, the flexible graphite becomes an excellent sealing material, which are made into various carbon mechanical seals with the effect of sealing components. These carbon mechanical seals are used in chemical, petroleum, electric power industries such as high temperature fluid seal.
Because the flexible graphite is formed by the expansion of expanded graphite after high temperature, the amount of intercalating agent remaining in the flexible graphite is very small, but not completely, so the existence and composition of the intercalation agent have a great influence on the quality and performance of the product.
Selection of Carbon Seal face Material
The original inventor used concentrated sulfuric acid as oxidant and intercalating agent. However, after being applied to the seal of a metal component, a small amount of sulfur remaining in the flexible graphite was found to corrode the contact metal after long term use. In view of this point, some domestic scholars have tried to improve it, such as Song Kemin who chose acetic acid and organic acid instead of sulfuric acid. acid, slow in nitric acid, and lower the temperature to room temperature, made from a mixture of nitric acid and acetic acid. By using the mixture of nitric acid and acetic acid as the inserting agent, the sulfur free expanded graphite was prepared with potassium permanganate as oxidant, and acetic acid was slowly added to nitric acid. The temperature is reduced to room temperature, and the mixture of nitric acid and acetic acid is made. Then the natural flake graphite and potassium permanganate are added to this mixture. Under constant stirring, the temperature is 30 C. After reaction 40min, the water is washed to neutral and dried at 50~60 C, and the expanded graphite is made after high temperature expansion. This method achieves no vulcanization under the condition that the product can reach a certain volume of expansion, so as to achieve a relatively stable nature of the sealing material.
Type |
M106H |
M120H |
M106K |
M120K |
M106F |
M120F |
M106D |
M120D |
M254D |
Brand |
Impregnated |
Impregnated |
Impregnated Phenol |
Antimony Carbon(A) |
|||||
Density |
1.75 |
1.7 |
1.75 |
1.7 |
1.75 |
1.7 |
2.3 |
2.3 |
2.3 |
Fractural Strength |
65 |
60 |
67 |
62 |
60 |
55 |
65 |
60 |
55 |
Compressive Strength |
200 |
180 |
200 |
180 |
200 |
180 |
220 |
220 |
210 |
Hardness |
85 |
80 |
90 |
85 |
85 |
80 |
90 |
90 |
65 |
Porosity |
<1 |
<1 |
<1 |
<1 |
<1 |
<1 |
<1.5 | <1.5 | <1.5 |
Temperatures |
250 |
250 |
250 |
250 |
250 |
250 |
400 |
400 |
450 |
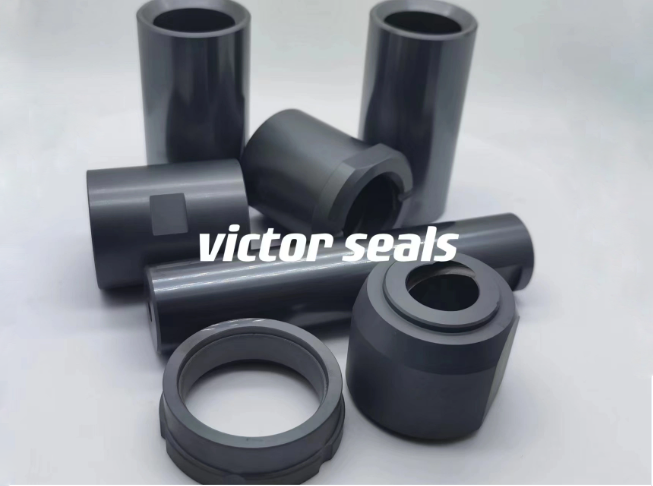
Silicon Carbide mechanical seals
Silicon carbide (SiC) is also known as carborundum, which is made of quartz sand, petroleum coke (or coal coke), wood chips (which need to be added when producing green silicon carbide) and so on. Silicon carbide also has a rare mineral in nature, mulberry. In contemporary C, N, B and other non-oxide high technology refractory raw materials, silicon carbide is one of the most widely used and economical materials, which can be called gold steel sand or refractory sand. At present, China's industrial production of silicon carbide is divided into black silicon carbide and green silicon carbide, both of which are hexagonal crystals with a proportion of 3.20 ~ 3.25 and microhardness of 2840 ~ 3320kg/m²
Silicon carbide products are classified into many kinds according to different application environment. It is generally used more mechanically. For example, silicon carbide is an ideal material for silicon carbide mechanical seal because of its good chemical corrosion resistance, high strength, high hardness, good wear resistance, small friction coefficient and high temperature resistance.
SIC Seal rings can be divided into static ring, moving ring, flat ring and so on. SiC silicon can be made into various carbide products, such as silicon carbide rotary ring, silicon carbide stationary seat, silicon carbide bush, and so on, according to the special requirements of customers. It can also be used in combination with graphite material, and its friction coefficient is smaller than alumina ceramic and hard alloy, so it can be used in high PV value, especially in the condition of strong acid and strong alkali.
SIC’s reduced friction is one of the key benefits of employing it in mechanical seals. SIC can therefore withstand wear and tear better than other materials, extending the life of the seal. Additionally, the reduced friction of SIC lessens the requirement for lubrication. Lack of lubrication reduces the possibility of contamination and corrosion, improving efficiency and reliability.
SIC also has a great resistance to wear. This indicates that it can endure continuous use without deteriorating or breaking. This makes it the perfect material for uses that demand a high level of dependability and durability.
It can also be re-lapped and polished so a seal can be refurbished multiple times over its lifetime. It is generally used more mechanically, such as in mechanical seals for its good chemical corrosion resistance, high strength, high hardness, good wear resistance, small friction coefficient and high temperature resistance.
When used for mechanical seal faces, silicon carbide results in improved performance, increased seal life, lower maintenance costs, and lower running costs for rotating equipment such as turbines, compressors, and centrifugal pumps. Silicon carbide can have different properties depending on how it has been manufactured. Reaction bonded silicon carbide is formed by bonding silicon carbide particles to each other in a reaction process.
This process does not significantly affect most of the physical and thermal properties of the material, however it does limit the chemical resistance of the material. The most common chemicals that are a problem are caustics (and other high pH chemicals) and strong acids, and therefore reaction-bonded silicon carbide should not be used with these applications.
Reaction-sintered infiltrated silicon carbide. In such material, the pores of the original SIC material are filled in the process of infiltration by burning out metallic silicon, thus secondary SiC appears and the material acquires exceptional mechanical properties, becoming wear-resistant. Due to its minimal shrinkage, it can be used in the production of large and complex parts with close tolerances. However, the silicon content limits the maximum operating temperature to 1,350 °C, chemical resistance is also limited to about pH 10. The material is not recommended for use in aggressive alkaline environments.
Sintered silicon carbide is obtained by sintering a pre-compressed very fine SIC granulate at a temperature of 2000 °C to form strong bonds between the grains of the material.
First, the lattice thickens, then the porosity decreases, and finally the bonds between the grains sinter. In the process of such processing, a significant shrinkage of the product occurs – by about 20%.
SSIC seal ring is resistant to all chemicals. Since no metallic silicon is present in its structure, it can be used at temperatures up to 1600C without affecting its strength
properties |
R-SiC |
S-SiC |
Porosity (%) |
≤0.3 |
≤0.2 |
Density (g/cm3) |
3.05 |
3.1~3.15 |
Hardness |
110~125 (HS) |
2800 (kg/mm2) |
Elastic Modulus (Gpa) |
≥400 |
≥410 |
SiC Content (%) |
≥85% |
≥99% |
Si Content (%) |
≤15% |
0.10% |
Bend Strength (Mpa) |
≥350 |
450 |
Compressive Strength (kg/mm2) |
≥2200 |
3900 |
Coefficient of heat expansion (1/℃) |
4.5×10-6 |
4.3×10-6 |
Heat resistance (in the atmosphere) (℃) |
1300 |
1600 |
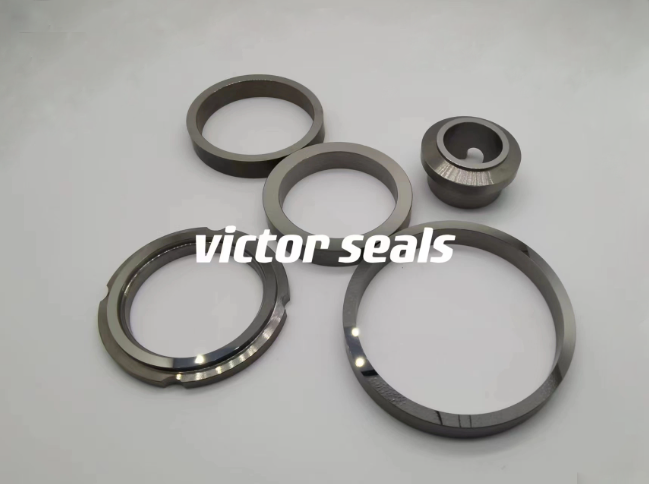
TC mechanical seal
TC materials have features of high hardness, strength, abrasion resistance and corrosion resistance. It is known as “Industrial Tooth”. Due to its superior performance, it has been widely used in military industry, aerospace, mechanical processing, metallurgy, oil drilling, electronic communication, architecture and other fields. For example, in pumps, compressors and agitators, Tungsten carbide ring are used as mechanical seals. Good abrasion resistance and high hardness make it suitable for the manufacture of wear-resistant parts with high temperature, friction and corrosion.
According to its chemical composition and usage characteristics, TC can be divided into four categories: tungsten cobalt (YG), tungsten-titanium (YT), tungsten titanium tantalum (YW), and titanium carbide (YN).
Tungsten cobalt (YG) hard alloy is composed of WC and Co. It is suitable for processing brittle materials such as cast iron, nonferrous metals and non-metallic materials.
Stellite (YT) is composed of WC, TiC and Co. Due to the addition of TiC to the alloy, its wear resistance is improved, but the bending strength, grinding performance and thermal conductivity have decreased. Because of its brittleness under low temperature, it is only suitable for high-speed cutting general materials and not for the processing of brittle materials.
Tungsten titanium tantalum (niobium) cobalt (YW) is added to the alloy to increase the high temperature hardness, strength and abrasion resistance through appropriate amount of tantalum carbide or niobium carbide. At the same time, the toughness also is improved with better comprehensive cutting performance. It is mainly used for hard cutting materials and intermittent cutting.
The carbonized titanium base class (YN) is a hard alloy with the hard phase of TiC, nickel and molybdenum. Its advantages are high hardness, anti - bonding ability, anti - crescent wear and anti - oxidation ability. At a temperature of more than 1000 degrees, it can still be machined. It is applicable to the continuous-finishing of alloy steel and quenching steel.
model |
nickel content(wt%) |
density(g/cm²) |
hardness(HRA) |
bending strength(≥N/mm²) |
YN6 |
5.7-6.2 |
14.5-14.9 |
88.5-91.0 |
1800 |
YN8 |
7.7-8.2 |
14.4-14.8 |
87.5-90.0 |
2000 |
model |
cobalt content(wt%) |
density(g/cm²) |
hardness(HRA) |
bending strength(≥N/mm²) |
YG6 |
5.8-6.2 |
14.6-15.0 |
89.5-91.0 |
1800 |
YG8 |
7.8-8.2 |
14.5-14.9 |
88.0-90.5 |
1980 |
YG12 |
11.7-12.2 |
13.9-14.5 |
87.5-89.5 |
2400 |
YG15 |
14.6-15.2 |
13.9-14.2 |
87.5-89.0 |
2480 |
YG20 |
19.6-20.2 |
13.4-13.7 |
85.5-88.0 |
2650 |
YG25 |
24.5-25.2 |
12.9-13.2 |
84.5-87.5 |
2850 |