Mechanical seals, components frequently utilized in various pump systems, play an integral role in preventing leakages and maintaining the system’s overall operational integrity. A common question that often arises is the necessity of seal water in these mechanical seals. This article delves into this intriguing topic, exploring the function of seal water within mechanical seals and determining if it’s a critical requirement for their optimal functioning. Journey with us as we decode this complex piece of machinery and its relationship with seal water, providing insights to engineers and hobbyists alike.
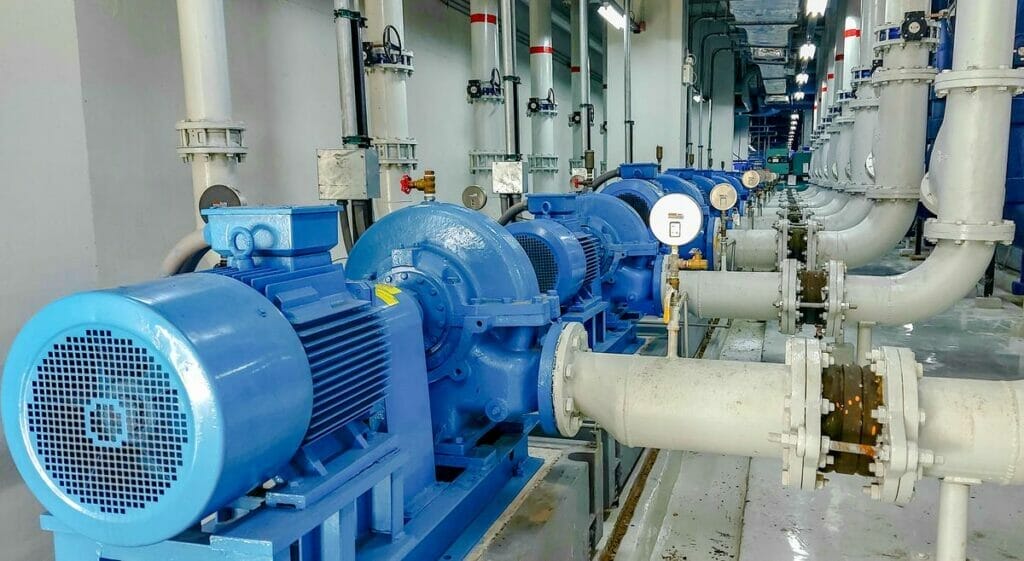
What is Seal Water?
Seal water, often known as barrier or flush water, is a crucial component used in the operation of several types of mechanical seals. Mechanical seals are indispensable for preventing leakage in rotating equipment like pumps and compressors. The seal water serves several functions – it lubricates the seals, removes heat generated during their operation, and aids in maintaining an optimal operational temperature.
In essence, a mechanical seal is a high-precision device designed to balance intricate forces. In this delicate balancing act, seal water plays two key roles: lubricant and coolant. As a lubricant, it helps minimize the direct contact between the sealing surfaces, thus reducing wear and tear and prolonging their lifespan. As a coolant, the seal water dissipates excessive heat from the sealing interface preventing any potential overheating that can cause catastrophic failure.
The Purpose of Seal Water
Seal water, also known as barrier water, plays a crucial role in the operation of mechanical seals. It is primarily used to create an optimum environment that ensures the smooth and efficient functionality of these seals. The fundamental purpose of seal water is to lubricate the seal faces, preventing friction and subsequent wear and tear.
The provision of a continuous cooling effect is another significant function performed by seal water. This aspect is incredibly essential because mechanical seals operate under varying degrees of temperature and pressure conditions. When these seals rotate at high speeds, they can generate substantial amounts of heat, potentially leading to damage or even failure if not adequately cooled.
Besides cooling and lubrication, using seal water helps maintain the reliability and extend the lifespan of mechanical seals by providing a supportive external environment. It assists in flushing away any accumulated debris or particles that may infiltrate the mechanical seal and inflict damage over time. In effect, introducing clean seal water aids in reducing possible contaminations in the system.
In highly corrosive applications where abrasive solids are involved, appropriate use of seal water serves as a shielding agent for mechanical seals against aggressive media present within certain systems. As such, its constant circulation can greatly reduce erosion or corrosion effects on installed components.
In principle, not all mechanical seals need seal water. However, the necessity of seal water largely depends on the nature of the application and operational conditions under consideration. When friction-generated heat becomes significant due to high speed or pressure differences, or when the sealed medium has poor lubricating properties or starts to crystallize at higher temperatures, additional cooling provided by seal water proves beneficial.
On certain occasions, certain mechanical seals may function effectively without any external flush like seal water at all. These cases primarily include applications involving conditions where process media offers sufficient lubricity for smooth operation and self-cooling capability.
However, it’s safer to state that most commonly-used mechanical seals do generally benefit from the usage of seal water due to its ability to maintain cooler surface temperatures during operation, ensuring sustained performance at peak efficiency levels over extended periods of time. Therefore, while it might not be an obligatory requirement for all circumstances, introducing seal water can certainly augment the durability and efficiency of many mechanical sealing systems.
One key takeaway: the decision on utilizing seal water should ideally be driven by careful examination of each corresponding application’s unique requirements – considering factors like operation pressure & temperature profiles, environmental regulations related to energy/water consumption & emission control and also material compatibility issues with respect to seal components and process fluid.
Applications Requiring Seal Water
There are numerous applications and industries that require the use of seal water in mechanical seals. These industries often deal with harsh environments, high pressures, or substances that could easily lead to wear or damage with the regular operation of machinery. Thus, the presence of seal water offers a protective layer for mechanical seals, prolonging their life-span and ensuring smooth operations.
One prominent industry is the oil and gas sector. Here, mechanical seals are often subjected to intense conditions resulting from processing raw materials. The abrasives found in crude oil can erode mechanical seals quickly; hence, the introduction of seal water creates a barrier between these damaging elements and the seal itself.
Then we have the chemical industry – another prominent user of seal water. In this case, it’s due to the wide range of corrosive chemicals handled which could considerably shorten a mechanical seal’s service life if not effectively protected.
In power generation plants too, specifically those dealing with thermal or nuclear energy production where extreme heat environments are commonplace – seal water plays a significant role in dissipating heat off from mechanical seals preventing any potential overheating situations that can derail operations.
The pharmaceutical and food processing sectors also often leverage seal water applications for hygienic reasons. Seal water helps reduce contamination risk by separating product process from any bearing oil leaks that could harm product safety standards.
Furthermore, pulp and paper manufacturers use seal water because they heavily rely on massive volumes of recycled water laden with solid particulates. Therefore introducing a constant flow of clean barrier fluid like seal water minimizes impeller wear occurrences due to abrasive solids present in such liquids.
These mentioned industries give us just a glimpse into numerous applications employing seal water as an integral part for sustaining robust operational performance of their mechanic equipment while significantly enhancing equipment longevity at large.
Advantages of Using Seal Water
The use of seal water in mechanical seals brings a myriad of benefits that enhances the overall efficiency and safety aspects of your system. This includes both operational and environmental perks.
Firstly, it’s crucial to emphasize that seal water helps maintain an optimal temperature within the sealing system. Its cooling effect prevents overheating, thus minimizing risks associated with seal damage and increasing the lifespan of your mechanical equipment, resulting in significant cost savings on replacements and repairs.
Secondly, using seal water fosters optimal lubrication, reducing friction between the mechanical seals’ faces and therefore hindering premature wear or degradation of these components. This can amplify the longevity and operational efficiency of your machinery.
Moreover, seal water can prevent harmful particles from making their way into the sealing interface. It acts as a barrier by flushing away abrasives which could potentially compromise the integrity of your mechanical seals if they were allowed to settle.
Finally, from an environmental perspective, using seal water aids sustainability efforts by controlling possible leakage. Mechanical seals are primarily designed to restrict fluid leakage around rotating shafts; however, an unintended consequence is often product loss and waste generation affecting both productivity and environmental compliance. By offsetting these leaks with clean water, you mitigate potential pollution incidents while supporting business-related corporate social responsibility initiatives.
In conclusion, though adding another element such as seal water may seem like complicating matters at first glance—its benefits regarding equipment reliability, operating efficiency improvement and ecological responsibility highlights its essential role in managing mechanical seals intelligently and responsibly.
In conclusion
In conclusion, mechanical seals indeed require seal water for their effective functioning. The intricate relationship between these two components cannot be overstated to ensure the longevity and efficiency of your machinery. The cooling and lubricating features of seal water protect against friction-related damages, promoting smooth, long-term operations. However, efficient management of seal water is equally important to prevent wastage and economic repercussions.
Post time: May-06-2024