The design and function of mechanical seals are complex, comprising several primary components. They are made of seal faces, elastomers, secondary seals, and hardware, each having unique characteristics and purposes.
The main parts of a mechanical seal include:
- Rotating Face (Primary Ring): This is the part of the mechanical seal that rotates with the shaft. It often has a hard, wear-resistant face made of materials like carbon, ceramic, or tungsten carbide.
- Stationary Face (Seat or Secondary Ring): The stationary face remains fixed and does not rotate. It is typically made of a softer material that complements the rotating face, creating a seal interface. Common materials include ceramic, silicon carbide, and various elastomers.
- Elastomers: Elastomeric components, such as O-rings and gaskets, are used to provide a flexible and secure seal between the stationary housing and the rotating shaft.
- Secondary Sealing Elements: These include secondary O-rings, V-rings, or other sealing elements that help prevent external contaminants from entering the sealing area.
- Metal Parts: Various metal components, such as the metal casing or the drive band, hold the mechanical seal together and secure it to the equipment.
Mechanical seal face
- Rotating seal face : The primary ring, or the rotating seal face, moves in tandem with the rotating machinery part, usually the shaft. This ring is often made from hard, durable materials such as silicon carbide or tungsten carbide. The design of the primary ring ensures that it can sustain the operational forces and friction generated during the machinery’s operation without deformation or excessive wear.
- Stationary seal face: In contrast to the primary ring, the mating ring remains stationary. It is designed to form a sealing pair with the primary ring. Although stationary, it is engineered to accommodate the movement of the primary ring while maintaining a strong seal. The mating ring is often made from materials such as carbon, ceramic, or silicon carbide.
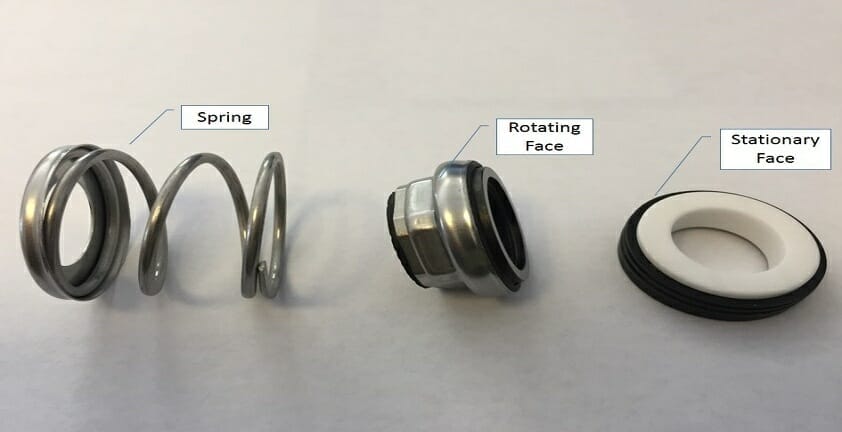
Elastomers (O-rings or bellows)
These elements, usually O-rings or bellows, serve to provide the necessary elasticity to maintain the seal between the mechanical seal assembly and the machinery’s shaft or housing. They accommodate slight shaft misalignment and vibrations without compromising the seal’s integrity. The choice of elastomer material depends on various factors, including temperature, pressure, and the nature of the fluid being sealed.
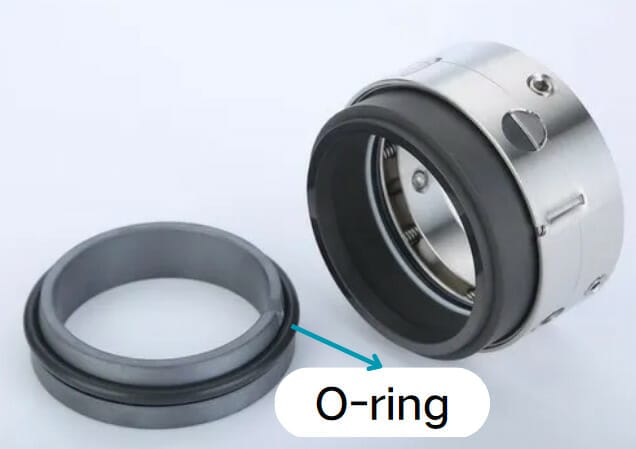
Secondary Seals
Secondary seals are components that provide a static sealing area within the mechanical seal assembly. They enhance the seal’s performance and reliability, especially in dynamic conditions.
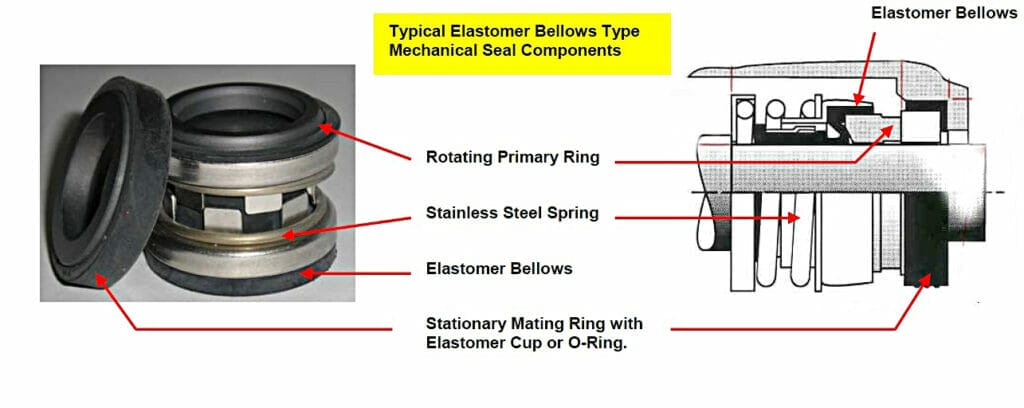
Hardware
- Springs: Springs provide the necessary load to the seal faces, ensuring constant contact between them even under varying operational conditions. This constant contact ensures a reliable and effective seal throughout the machine’s operation.
- Retainers: Retainers hold various components of the seal together. They maintain the correct alignment and position of the seal assembly, ensuring optimal performance.
- Gland plates: Gland plates are used to mount the seal to the machinery. They support the seal assembly, keeping it securely in place.
- Set screws: Set screws are small, threaded components used to secure the mechanical seal assembly to the shaft. They ensure that the seal maintains its position during operation, preventing potential displacement that could compromise the seal’s effectiveness.
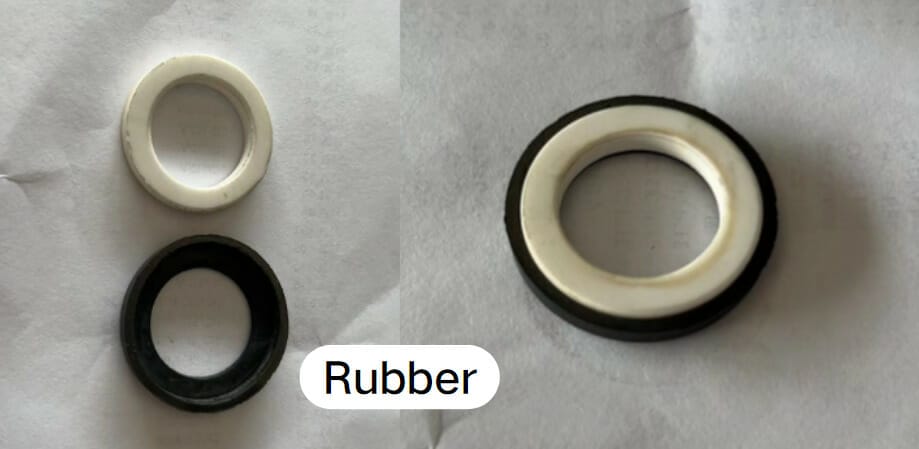
In conclusion
Each component of a mechanical seal plays a critical role in the effective sealing of industrial machinery. By understanding the function and importance of these components, one can appreciate the complexity and precision required in designing and maintaining efficient mechanical seals.
Post time: Dec-22-2023